About
Quality
Intensive integrated management system
1. Identification and conversion of customer requirements
APQP is responsible for early product planning, converting all customer requirements into operable and executable requirements and measures, and following up on the implementation of customer requirements by training the execution department.
2. Supplier management
The SQE department is responsible for the systematic management of suppliers so that the entire supply chain has a common sense of responsibility and mission and shares the results of rapid development to achieve a win-win situation between supply and demand.
3. Process quality control
Establish a systematic quality management system, based on standard work instructions, and set up a complete training mechanism to ensure standard operation, equipment maintenance, change and exception management, continuous optimization and advancement management, and key control items in the control process. Product quality requirements.
4. Take quality control measures
Strictly control quality, from testing equipment, staffing and standard implementation to inspection and control of quality assurance, and take quick and effective improvement measures in exchange for customer feedback on quality abnormalities.
5. Continuous improvement
Incorporate, apply and improve continuous improvement work as part of the system to create and establish a corporate culture of continuous improvement.
6. Customer service
With the customer as the center, we improve customer satisfaction from the aspects of management mechanism, corporate culture, system guarantee, etc., in order to achieve the purpose of enhancing Dinghua Xintai's visibility, reputation and customer loyalty.
Testing Equipment
CMI-900 gold thickness tester
AVI appearance inspection machine
CMI-700 copper thickness tester
Three dimensions
Mitutoyo sj-210
Four-wire flying probe test machine
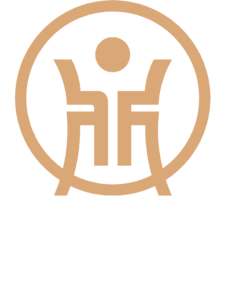

Product service
News
Contact us
- 13556897093
- 0755-29877925
- cer@pcbbest.com
- No. 7 and 9, Xinfa 2nd Road, Xinfa Industrial Zone, Xinqiao Street, Baoan District, Shenzhen City